Mapping an Underground, Waterlogged Mine with LiDAR
Underground mines can be extremely dangerous. The Nexa Vazante mine has one of the highest flows of water in Latin American mines. This makes mapping with mining drones difficult, which is a concern as this method is used to increase personnel safety.
The high humidity from the water content can cause condensation in the LiDAR scanner, decreasing the amount of information captured and interfering with SLAM navigation. The water also pools, forming large reflective areas that can cause laser mirroring and reflectance. Both make it challenging to use LiDAR scanners and autonomous mining drones to capture the data for measuring and extracting topographical and geotechnical information. Despite these obstacles, the mine operation achieves record-breaking levels of zinc extraction, driving the need for a smart, highly efficient solution.
Searching for a mining drone technology that could bring security and accessibility to the workflow, Nexa Resources tried many options, but none could reliably deliver the desired results. The company reached out to Brazilian-based Emesent partner Gestão Engenharia.
For the demonstration, Nexa identified two areas to be captured within the mine. The first was a waterlogged area, and the second a tight drift containing machinery and a pile of material that led to a stope.
Gestão Engenharia and Emesent Technical Specialist, Clayton da Silva, made their way to the mine, located about 8.5 km from the municipality of Vazante in the state of Minas Gerais, Brazil, to demonstrate Hovermap’s abilities.
For the waterlogged environment, Clayton was scanning to capture information on the gallery walls and the exposed ground. To do this, he mounted Hovermap on a drone and avoided flying close to the reflecting pools. To reduce the humidity of the light pack, he kept the LiDAR at room temperature with a flannel cover until the moment of the flight to reduce any condensation.
Within five minutes, Clayton and the Hovermap had captured robust and reliable data of the walls and ground.
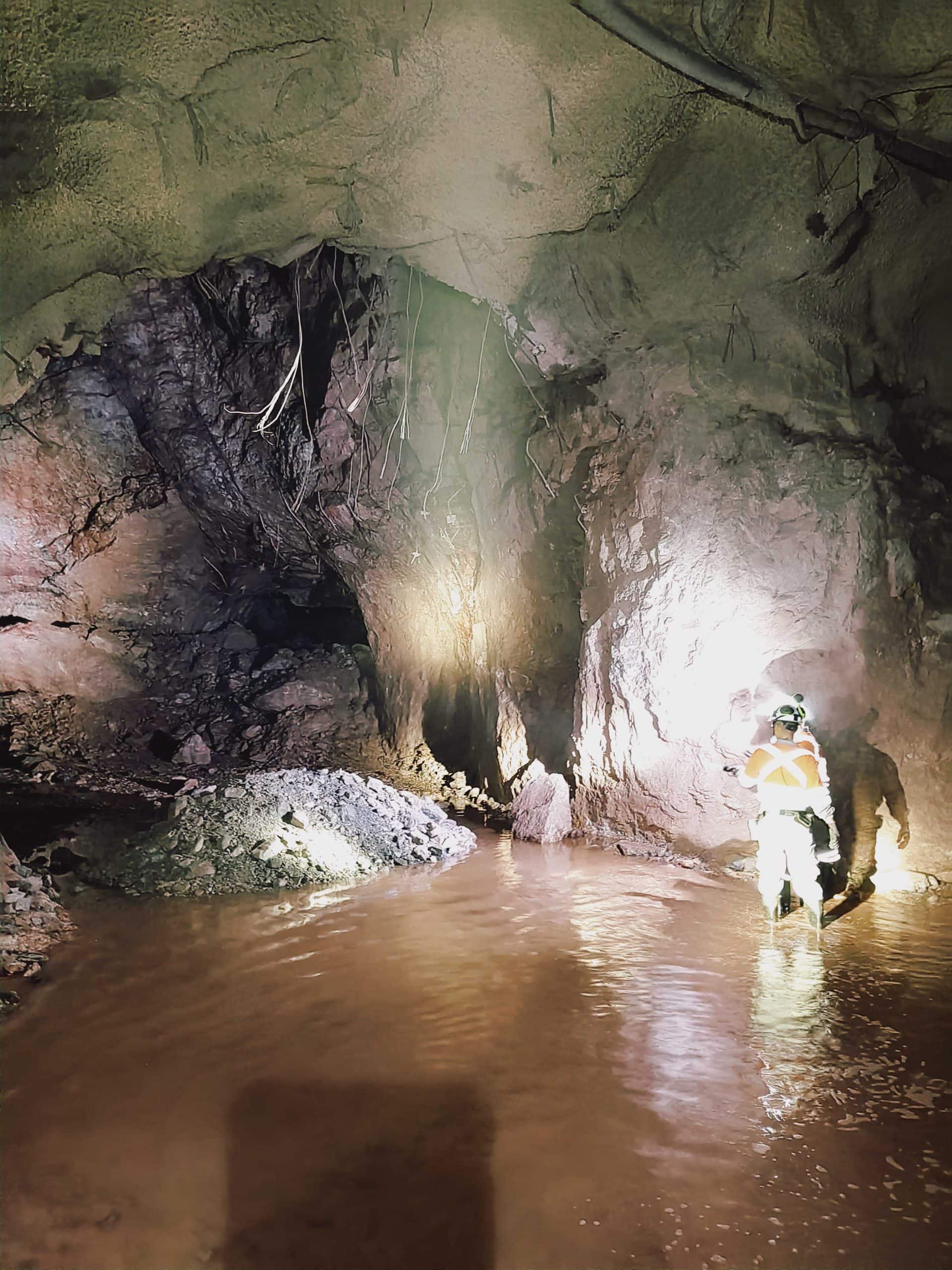
For the second test area, the stope was beyond the pile of material. Clayton used a drone-mounted Hovermap in Pilot Assist mode. This capability provides the operator with omnidirectional collision avoidance. Pilot Assist mode acts as a safety bubble for the drone and assists the pilot in keeping the asset and the equipment safe while ensuring a stable flight.
The video below shows the path to the stope was essentially an obstacle course that Clayton navigated with the help of Hovermap. After capturing the stope and some specific images requested, Clayton confirmed the entire stope had been mapped using the real-time point cloud on the tablet. He then used the Return to Home feature, and at the push of a button, Hovermap autonomously navigated out of the stope and returned to the take-off point.